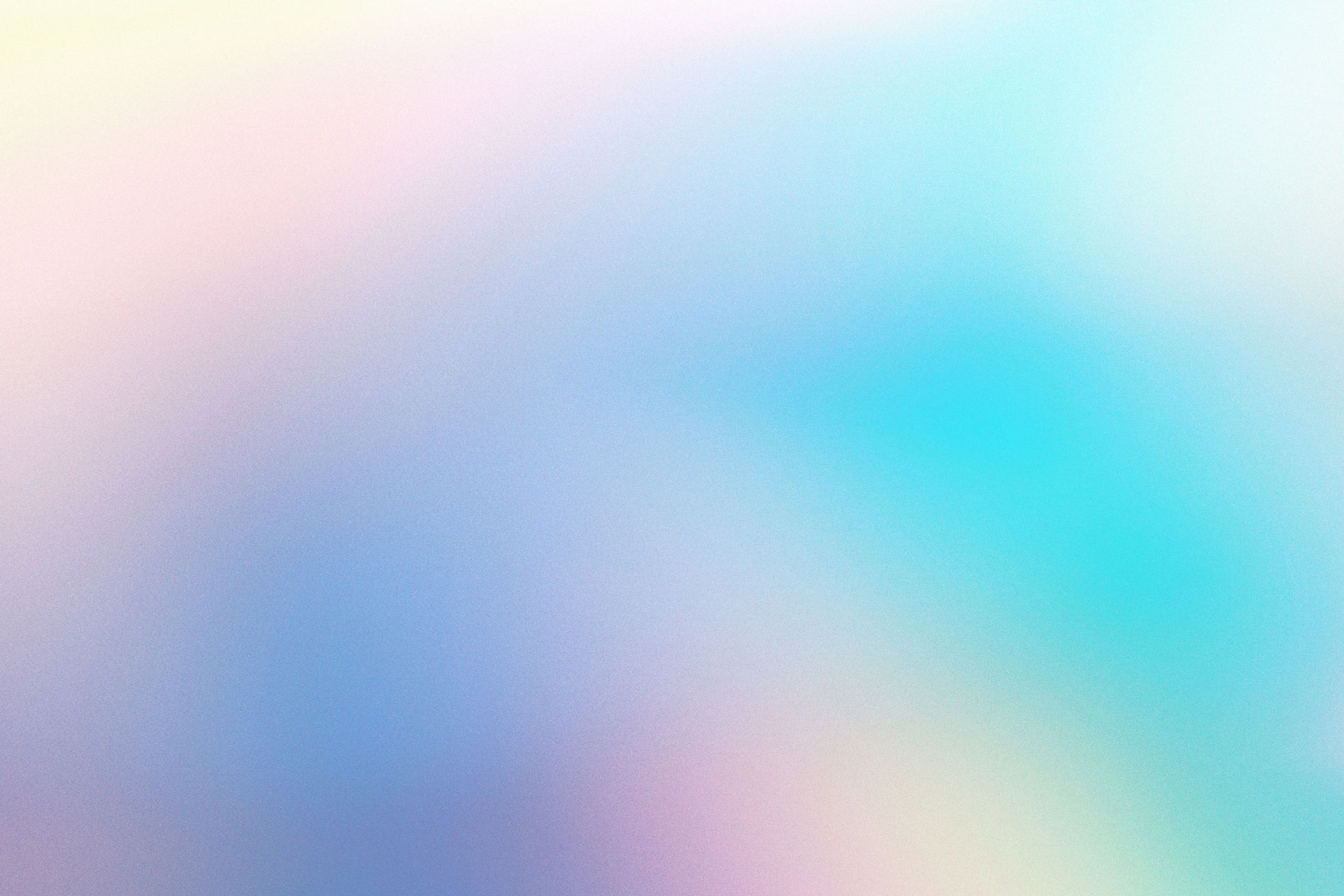


SP & PT versions under construction
HVO
Hydrotreated Vegetable Oil

Sustainable transport biofuels provide low carbon intensity mobility to the legacy fleet and will become more important in shipping & aviation in the future. Biodiesel, bioethanol, and HVO (hydrotreated vegetable oil) / HEFA (hydrotreated esters & fatty acids) are already widely used and provided 3% of transport energy globally in 2017 [IEA, 2020].
Even though the costs of using sustainable fuels are projected to be higher than alternatives in the long term, the use of 100% renewable diesel, such as HVO (a.k.a. green or renewable diesel), can achieve comparable life-cycle GHG reduction to the use of electric vehicles (EVs), allowing for faster decarbonization of existing fleets in the short term [MKY, 2022].
Diesel-like
HVO is a diesel-like fuel produced w/o fossil resources by processing lipids like plant oils, animal fats, or waste cooking oil. It is a paraffinic fuel, which are an alternative to diesel w/ low sulfur & aromatics content. HVO has about 7% less fuel density, but higher cetane number (88 to 95) compared to diesel fuel (48 to 50), an indicator of the combustion speed of the fuel. HVO can be blended with diesel in any proportion, which is particularly beneficial in standby genset applications, where stored fuel consumption is low [CM, 2022].
Synthesis
While HVO (spec: EN 15940) is derived from the same feedstock used to produce biodiesel (whose molecules are mainly FAME - fatty acid methyl ester - spec: EN 14214 in Europe, ASTM D6751 in the U.S.), it is produced via a hydrotreated process (instead of transesterification, applied to FAME), which helps improve its oxidation stability, avoiding bacterial growth (that occurs in biodiesel), and provides better storage stability and better cold flow properties [CM, 2022] [MW, 2023].
In addition, HVO can be used in both standby & prime applications, whereas biodiesel is better suited to prime applications [CAT, 2023]. Figure 1 shows the production route of straight vegetable oil (SVO - requires modification on diesel engines), biodiesel, and HVO. Figure 2 details the last two.
Figure 1: Production route of SVO, biodiesel, and HVO

Figure 2: HVO and biodiesel production routes
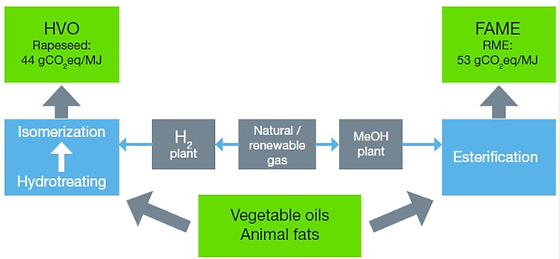
Pre-treatment
The HVO process requires efficient, flexible, safe, reliable, and sustainable pre-treatment of feedstocks to remove impurities such as phosphorous, metals, polyethylene, nitrogen, sulfur and chlorine-containing components that are naturally present in raw materials. An efficient & flexible pre-treatment process will determine if a low-quality feedstock can be used, which will directly impact the viability of the HVO plant [BDD, 2023]. Figure 3 shows the basic configuration of a HVO pre-treatment plant.
​
Production
In 2020, Europe had the largest HVO capacity worldwide, at 3.5 mi mt (vs 1.9 mi mt of North America). Global investment in liquid biofuels more than doubled in 2021, reaching just over USD 8 bi, 2/3 of this growth driven by bio-based diesel, spurred by rising investment in HVO, which represented 16% of biodiesel consumed globally in 2021 [IEA, 2022] [IFP, 2022]. HVO capacity in North America is forecast to surpass Europe, reaching 12.6 mi mt by 2025 [STAT, 2023], as shown in Figure 4.
Figure 3: Basic configuration of a HVO pre-treatment plant

Figure 4: Worldwide HVO production - 2025 forecast
